KAPAKBET cara mudah dan cepat untuk mengakses game SLOT GACOR favorit Anda di Kapakbet, Nikmati pengalaman bermain SLOT GACOR77 terbaik dengan deposit via SLOT QRIS yang praktis dan peluang menang besar setiap hari.
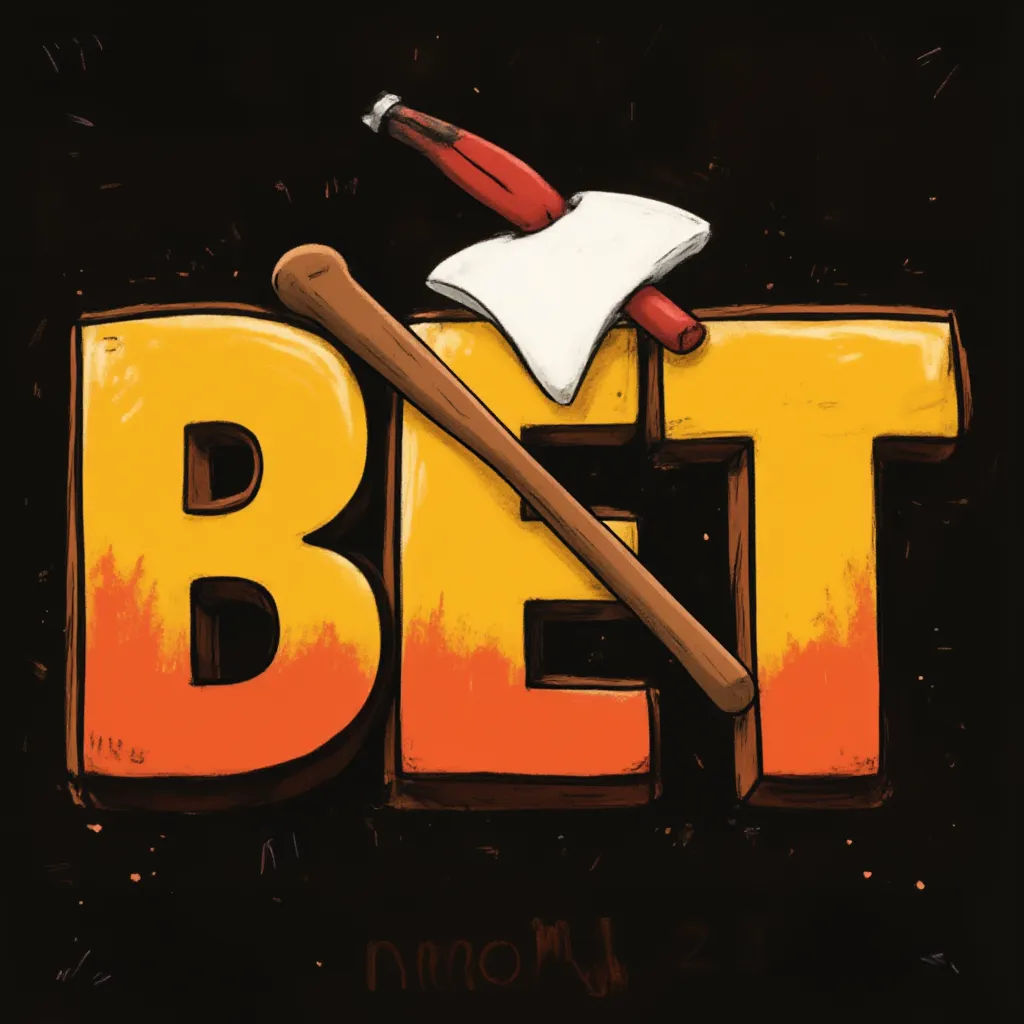
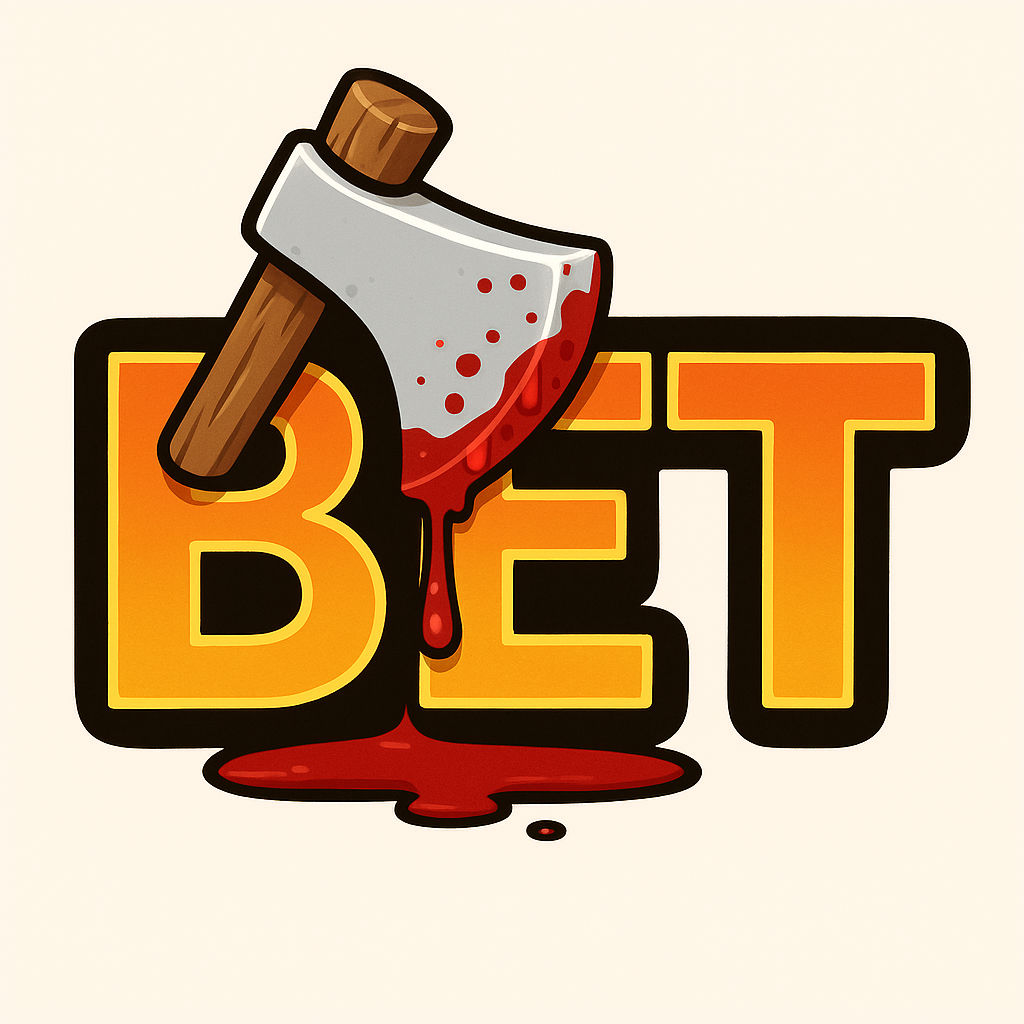
KAPAKBET cara mudah dan cepat untuk mengakses game SLOT GACOR favorit Anda di Kapakbet, Nikmati pengalaman bermain SLOT GACOR77 terbaik dengan deposit via SLOT QRIS yang praktis dan peluang menang besar setiap hari.